Pouring Heat: The writer/artist (left) and sculptor Sean Monaghan pour bronze into ceramic molds.
Bronze tools led early humans toward civilization. Through art, bronze continues to define modern culture
By John Yewell
Photographs by George Sakkestad
IT WAS AN EIGHTH-GRADE shop teacher who introduced me to lost-wax bronze casting, back in the days before arts programs were gutted from the public school curricula. I remember the beautiful little horses, about the size of your hand, he made in wax. He showed me how to encase the figures in plaster, melt out the wax and then pour in the molten bronze. When he broke away the plaster to reveal the bronze horses inside, it was like a magic trick. Voilá!
My own first foray in his class was a tiny bronze incense burner. (Hey, it was the '60s, OK?) Later, I would try more complicated forms and ideas. When I got to UCSC and discovered the sculpture facilities, I thought I'd died and gone to heaven--even though the casting area then was nothing more than a sand pit in the floor of a leaky barn near the main entrance to campus.
There is a primitiveness to bronze casting, a throwback to an early era of human civilization that defies modern conveniences. The process of creating bronze is the antithesis of the "clean room" so necessary to the production of computer chips. You get to play with a variety of tools and materials and just plain get dirty. There is something romantic about getting dirty in the production of art.
I also love the tactile quality of the metal, the cool smoothness, versatility and strength of the material that allows you to make almost anything with it. The surface of a bronze figure is as close to human skin as the art gods have yet devised.
Alas, bronze sculpture did not become my life's work. Sean Monaghan was luckier.
Monaghan says he discovered bronze when a friend encouraged him to take a sculpture class in 1980 at UCSC. He was an undeclared major at the time, but he says he realized right away that he had found his calling.
"I didn't want to be an art major--it seemed so impractical," Monaghan says. "But I knew sculpture was where I had been going all along."
Monaghan graduated with a sculpture degree in 1983, but it wasn't until 1992 that he and friend Roger Knapp were able to start Bronze Works. For the first year or so Monaghan had to continue doing home remodeling jobs on the side to support himself.
Located on Coral Street in Santa Cruz, Bronze Works is the only independent commercial bronze foundry in the county, and Monaghan is a busy guy.
"I'm usually working for about 25 people at a time," Monaghan says, and pouring about 100 pounds of bronze a week and 20 to 30 pieces a month. Demand has allowed him to pick and choose clients, and he says he prefers projects on which he can have "some creative input." It also allows him to make time for his own work and to finish his master's in fine arts degree at San Jose State University.
What attracted him to bronze?
"Bronze is also a very functional material. It's very process oriented and requires some technical prowess. I like the variety of tools and options," Monaghan says.
"Also," he adds, "it lasts forever, and you can make just about anything. With stone, you can't do long skinny tendrils. Bronze can take a lot of different colors and forms. The metal has a luster and is almost translucent. It can appear light or heavy; it can be polished. With patinas [chemical coloration], you can get a rich surface."
Just don't ask him to bronze those baby shoes--that's a plating process better done through a trophy shop.
When I go to a museum, I make a beeline for the bronze exhibits, and every few years or so I make something in wax and have it cast in bronze. Monaghan and the Bronze Works gave me the opportunity to create a small piece, a kind of coffee-table surfer, and to follow the production to completion in this photo essay.
How To
HERE ARE SEVEN basic steps in the casting of bronze. Extra steps are added if a permanent mold of polyurethane or silicone rubber is made of the sculpture so that it can be reproduced. Although the mold-making process has been skipped here, Monaghan says he makes "lots of molds."
Above, Sean Monaghan holds the original sculpture, made of a malleable brown material called microcrystalline wax.
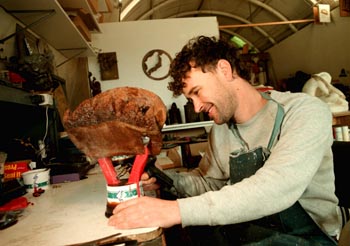
1. Gating: Preparing the Sculpture for Casting
A bronze sculpture usually starts out as wax. Either it is sculpted originally in wax, or wax is used to copy a figure made in clay, plaster or other materials.
Before step two, when the wax original will be encased in a ceramic shell, wax "gates" must be added, using a hard red wax. When the wax is melted out of the plaster, these gates provide a conduit through which the bronze can flow to all parts of the sculpture. Think of the wax as negative space that creates a hole in the ceramic into which the bronze will be poured.
2. The Ceramic Shell
The sculpture and its gates are now dipped about 10 times into colloidal silica, or ceramic slurry. After each coating, the wet ceramic is sprinkled with silica stucco (shown at left) to give the next coat something to adhere to. It is allowed to dry from two to five hours between coats and ultimately achieves a thickness of about three-eighths of an inch.
The ceramic is porous, so during the pouring of the bronze, gases can escape through the shell. In another method of casting, called plaster investment, the gating process is much more complicated because extra wax called "vents" must be attached to the sculpture to allow gas to escape. Ceramic shell casting has the added advantage of being able to reproduce highly detailed work with less "flashing," the spread of hot bronze into cracks in the plaster during pouring.
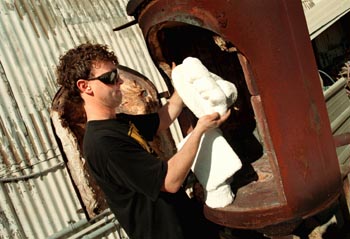
3. Burn Out
The shell is then placed in an oven or kiln and baked at around 1,800 degrees for 15 to 30 minutes, depending on the size of the shell. The wax melts out (about 90 percent is recycled), and the shell is hardened. It is allowed to cool for 30 to 60 minutes. Inside is left the cavity into which the bronze will be poured.
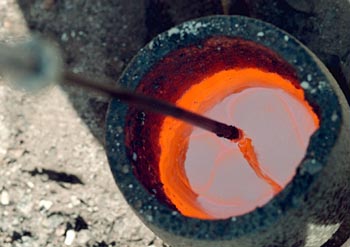
4. Melting the Bronze
Bronze is an alloy composed primarily of the basic element copper. Some alloys include zinc, but more common in sculpture is a composition of 94 percent copper, 4 percent silicon, 1.5 percent manganese, and trace elements such as iron and aluminum. This "silicon bronze" is the type used at the Bronze Works.
It is melted at 1,900 to 2,100 degrees in a silicon-carbide crucible. The temperature depends on the sculpture--pieces with finer detail need hotter metal to fill those details. Impurities (dross, usually bits of other metals and glass from silicon formed in the heat) are skimmed off the top.
5. Pouring the Bronze
Pouring usually takes place a day after the burn out. Before the bronze is poured in, the shell is reheated for a few minutes at a couple of hundred degrees so it is warm when the hot bronze is poured. The shell is then placed on a rack near the furnace where the bronze is being melted.
Two people using giant tongs reach down in the furnace, pull the crucible out and set it into a pouring shank. This is a round metal holder attached to two bars. One person turns the shank, which tilts the crucible and pours the liquid bronze into the ceramic shell. The metal must be poured rapidly before it cools. If more than one piece is being poured at once, the sculpture with the thinnest parts will be poured first.
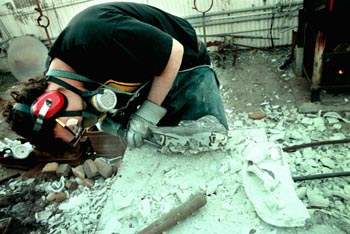
6. Break Out
The metal hardens within minutes but is left to cool for at least an hour before the ceramic shell is broken away. The shell is thin but very hard, so it has to be smashed or air chiseled off, depending on the delicacy of the bronze piece inside. The leftover ceramic material, which is similar to a smashed sink or toilet, can be recycled as underlayment in road construction.
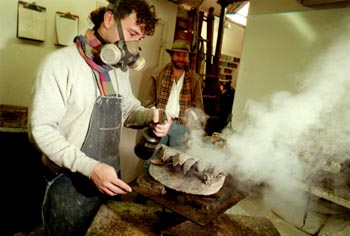
7. Finishing
After the shell is broken away, the sculpture is sandblasted to remove the final bits of ceramic. Then the gates are cut away (this bronze is reused) and minor imperfections such as bumps or small holes are fixed by welding, chiseling and other abrasive techniques. The cleaned surface of the piece is then ready for the final step.
Now a patina (coloring) can be applied. This is done by heating the sculpture and spraying the surface with chemicals (above). Formulas for a wide range of colors are available.
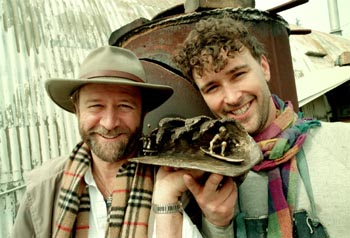
Done!
The writer/artist (left) and Monaghan show off the final product.
[ Santa Cruz Week | MetroActive Central | Archives ]